فولاد خام ایران در جایگاه نهم تولید جهانی قرار گرفت
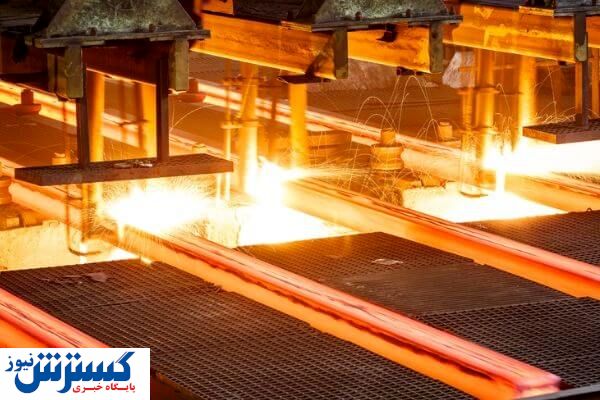
در طول نخستین ماه سال 2024 میلادی، ایران با رشد 39.3 درصد، بالاترین رشد در تولید فولاد خام را در میان 10 کشور برتر جهان به ثبت رساند.
این اطلاعات از گزارش جدید انجمن جهانی فولاد است که فهرست 10 کشور برتر تولیدکننده در ماه ژانویه 2024 را منتشر کرده است. با تولید 2 میلیون و 600 هزار تن فولاد خام، ایران در جایگاه نهم این فهرست قرار گرفته است.
71 کشور جهان در ماه ژانویه، 148 میلیون و یکصد هزار تن فولاد خام منتشر کردند که در مقایسه با تولید مدت مشابه سال گذشته میلادی، 1.6 درصد کاهش نشان می دهد.
10 کشور برتر تولیدکننده فولاد خام در ماه ژانویه 2024 به ترتیب شامل چین (77.2 میلیون تن، کاهش 6.9 درصدی)، هند (12.5 میلیون تن، افزایش 7.3 درصدی)، ژاپن (7.3 میلیون تن، افزایش 6 دهم درصدی)، آمریکا (6.8 میلیون تن، کاهش 3 دهم درصدی)، روسیه (6.2 میلیون تن، افزایش 1.2 درصدی)، کره جنوبی (5.7 میلیون تن، افزایش 1.5 درصدی)، ترکیه (3.2 میلیون تن، افزایش 24.7 درصدی)، آلمان (2.9 میلیون تن، کاهش 9 دهم درصدی) ایران (2.6 میلیون تن، افزایش 39.3 درصدی) و برزیل (2.5 میلیون تن، کاهش 7.2 درصدی) است.
روشهای تولید فولاد خام
با توجه به تنوع موارد استفاده فولاد در دنیا و گسترده شدن دایره مصرف فولاد با پیشرفت فناوری، تولید فولاد و نیز همگام با پیشرفت فناوری تغییرات بسیاری داشته است، که در پی این تغییرات تولیدکنندگان سعی در بالا بردن بهرهوری و استفاده از انرژی و سوختهای ارزانتر با توجه به محیط جغرافیایی خودکردهاند.
روشهای تولید فولاد خام
امروزه فنآوریهای مورداستفاده در تولید محصولات فولادی در مراحل بعد از به دست آوردن فولاد مذاب یعنی ریختهگری و نورد، کموبیش یکسان است. اما برای به دست آوردن فولاد مذاب یا خام، از فنآوریهای مختلفی میتوان استفاده کرد.
بهطورکلی فولاد خام از دو روش زیر تولید میگردد:
1- تهیه آهن خام یا چدن مذاب در کوره بلند (BF) و تولید فولاد در کانورترهای اکسیژنی، نظیر ذوبآهن اصفهان.
2- احیای مستقیم سنگآهن (DR) و ذوبآهن اسفنجی (DRI) و قراضه (Scrap) در کورههای الکتریکی از قبیل قوس الکتریکی (EAF) نظیر فولاد خوزستان یا القایی (IMF)، نظیر مجتمع فولاد جنوب.
لازم به ذکر است که تولید فولاد از روشهای دیگری نظیر روش کوره باز (Open Heart) نیز انجام میگیرد که با توجه به حجم تولید بسیار محدود آن در جهان، که طبق آمار World Steel حدود 5/2درصد از کل تولید فولاد جهان در سال 2007 بوده است و کاهش پیوسته تولید از این روش، در اینجا موردبررسی قرار نمیگیرد.
درروش اول که شیوه سنتی تولید است، از احیای غیرمستقیم آهن استفاده گردیده، سنگآهن دانهدرشت و سنگآهن پس از فرآوری و تبدیل به آگلومره به همراه آهک و کک وارد کوره بلند شده، آهن خام یا چدن مذاب (Pig Iron) به دست میآید. در مرحله بعد آهن خام در یک کانورتر به فولاد مذاب تبدیل گردیده، کربن و ناخالصیهای دیگر آن به کمک اکسیژن خارج و فولاد خام (Crude Steel) تولید میگردد.
روش دوم تولید فولاد، استفاده از کورههای الکتریکی و ذوب مجدد قراضه آهن و فولاد هست. به دلیل کمبود منابع قراضه در جهان و نیز رشد فزاینده قیمت آن در طول سالهای گذشته، در این روش میتوان به همراه قراضه از آهن اسفنجی نیز برای ذوب در کوره استفاده نمود.
آهن اسفنجی
آهن اسفنجی محصول عملیات احیای مستقیم سنگآهن است که دارای عیار بالای آهن بوده، جایگزین مناسبی برای قراضه جهت ذوب است. تولید آهن اسفنجی از سنگآهن، عموماً به دو روش گازی (Gas Based) یا استفاده از زغالسنگ (Coal Based)، برای احیای آهن صورت میپذیرد. معمولاً در کشورهایی که دارای ذخایر گاز هستند، از روش گازی استفاده میگردد. در ایران نیز بهطور مثال، فولاد خوزستان و فولاد مبارکه از گاز بهعنوان ماده احیاکننده استفاده میکنند. شناختهشدهترین روشهای احیای مستقیم گازی روشهای میدرکس و HYL هستند. شرکت MMTE ایران و نیز شرکت ایریتک دارای لیسانس ساخت کارخانههای احیای مستقیم (از کوبه استیل ژاپن) با فناوری میدرکس هستند (میدرکس فناوری اصالتاً آمریکایی هست
3/66درصد فولاد خام جهان به کمک روش کوره بلند و 2/31درصد آن نیز به روش احیای مستقیم و استفاده از کورههای الکتریکی تولید میگردد. باوجودآنکه بیشتر تولید فولاد خام در جهان بهوسیله روش کوره بلند تولید میشود، اما موارد ذیل استفاده از روش احیای مستقیم و کورههای الکتریکی را، مخصوصاً در ایران، توجیهپذیرتر میکنند:
- با توجه به استفاده از قراضه آهن، این روش سریعتر است.
- هزینه راهاندازی یک واحد کوره بلند نسبت به یک واحد احیای مستقیم و کوره الکتریکی در ظرفیتهای متناظر، بالاتر است. بهطور مثال در محاسبات شرکت ملی فولاد، میزان سرمایهگذاری موردنیاز، به ازای تولید هر تن فولاد با توجه به مفروضات ذیل انجام میگیرد:
کوره بلند (شامل کک سازی، آگلومراسیون، کوره بلند، کانورتر و ریختهگری مداوم شمش) 510 دلار
روش دیگر (شامل گندلهسازی، احیای مستقیم، کوره قوس الکتریکی و ریختهگری مداوم شمش) 430 دلار
- کک متالورژیکی که یکی از مواد اولیه موردنیاز کورههای بلند است، از زغالسنگ کک شو به دست میآید که منابع آن در ایران محدود است. همچنین این ماده عمدتاً وارداتی و گرانقیمت است. برای تولید هر تن آهن خام به روش کوره بلند، طبق استانداردهای جهانی به حداقل 5/1 تن سنگآهن و 450 کیلوگرم کک متالورژیکی نیاز بوده که گاهی این مقدار تا 3 تن سنگآهن و 1000 کیلوگرم کک هم افزایش مییابد. درنتیجه با توجه به آنکه میتوان از گاز بهعنوان ماده احیاکننده درروش احیای مستقیم استفاده نمود و باوجود منابع عظیم گاز در ایران، عملاً روش کوره بلند مزیت خود را از دست میدهد.
- روش کوره بلند محدودیتهای زیستمحیطی بیشتری نسبت به روش احیای مستقیم دارد.
- آهن اسفنجی عیار بالاتری نسبت به آهن خام دارد.
- کوره بلند در ظرفیتهای بالا (حداقل یک و نیم میلیون تن در سال) دارای توجیه اقتصادی بیشتری است، درحالیکه از روش احیای مستقیم میتوان در واحدهای کوچک فولادسازی نیز با توجیه اقتصادی مناسب استفاده کرد.
- آهن اسفنجی را میتوان بهصورت آهن گرم کلوخه شده (HBI) درآورده، به سهولت حمل یا ذخیره کرد. درصورتیکه که حمل آگلومره که خوراک کوره بلند است سختتر هست.
- در فرآیند احیای مستقیم میتوان از گاز طبیعی بدون حذف ناخالصیهای آن استفاده کرد.
درعینحال شرکتهای ذوبآهن اصفهان، فولاد میبد، فولاد زاگرس، ذوبآهن غرب کشور و فولاد زرند طبق برنامه چهارم توسعه، درمجموع حدود 5 میلیون تن فولاد، از طریق روش کوره بلند تولید خواهند کرد که با توجه به پتانسیلهای موجود در کشور، به نظر کافی میآیند.