هستهای در صنعت -9| انقلاب کامپوزیتها با فناوری هستهای
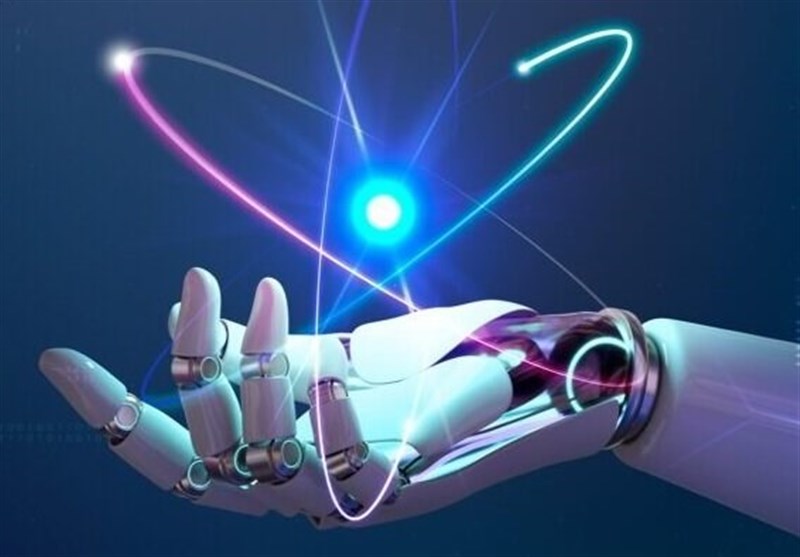
ورود فناوری هستهای به قلمرو تولید مواد کامپوزیتی، فصل تازهای از انقلاب صنعتی را رقم زده است؛ تابش کنترلشده نوترونی و گامایی میتواند خواص مکانیکی، حرارتی و ساختاری مواد را بازتعریف کند.
خبرگزاری تسنیم؛ گروه اقتصادی دنیای فناوری مواد، همواره با آرزویی مهم همراه بوده است: طراحی موادی که در عین سبکوزنی، مقاومت بالا، دوام حرارتی، و شکلپذیری مناسب داشته باشند. این رؤیا در عصر حاضر، بیش از هر زمان دیگر به واقعیت نزدیک شده و یکی از بازیگران اصلی این تحول، فناوری هستهای است. در زمانی که رقابت در صنایع هوافضا و خودروسازی، دیگر نه فقط حول محور طراحی، بلکه بر مبنای کیفیت مواد و قابلیتهای فنی آنها میچرخد، ورود ابزارهای نوین مبتنی بر پرتودهی، ایزوتوپهای پایدار، و شتابدهندههای ذرهای، نظم جدیدی را بر مهندسی مواد حاکم کرده است.
در حوزه صنایع فضایی، نیاز به موادی که بتوانند در برابر تابش کیهانی، شوکهای حرارتی، و فشارهای شدید مقاومت کنند، روزبهروز افزایش مییابد. در چنین شرایطی، استفاده از فناوریهای پرتوی برای اصلاح ساختار داخلی مواد کامپوزیتی، راهی کمهزینه و مؤثر برای ارتقاء عملکرد آنها به شمار میرود. همچنین در صنعت خودروسازی، که بهطور فزایندهای بهدنبال کاهش وزن خودروها بدون قربانی کردن ایمنی و دوام است، مواد کامپوزیتی پرتودهیشده پاسخی نوآورانه ارائه میکنند.
تکنولوژی هستهای، برخلاف تصور رایج که آن را محدود به تولید برق یا مصارف نظامی میداند، در حوزه مواد کامپوزیتی نقشی بیبدیل ایفا میکند. از پرتودهی گاما برای بهبود پلیمریزاسیون رزینها، تا استفاده از نوترونها برای مهندسی خواص مکانیکی یا شتابدهندهها برای ایجاد پیوندهای مولکولی قویتر، هر کدام از این ابزارها توانستهاند جنبهای از چالشهای قدیمی صنعت را حل کنند.
در همین زمینه بیشتر بخوانید
تشخیص خوردگی در لوله های نفت و گاز تعیین ترکیب آلیاژهای فلزی با پرتودهی تشخیص نشت مخازن پرفشار با رادیوایزوتوپها آشکارسازی ترکهای درونی و زیرسطحی کنترل کیفیت جوش با پرتو گامادر این یادداشت پس از معرفی فناوری، بیان اصول، اجزا، فرآیندها، کاربردها، مزایا و چالشها تا ارائه نمونهها و چشمانداز آینده تنظیم شده تا به خواننده درک روشن و یکپارچهای از این تحول علمی و صنعتی بدهد.
معرفی و اصول کلی فناوری
فناوری استفاده از تابش هستهای در تولید و بهبود مواد کامپوزیتی بر مبنای دو اصل بنیادی استوار است: نخست، تأثیر پرتوهای یونیزان (مانند گاما یا نوترون) بر ساختار مولکولی مواد پلیمری یا فلزی، و دوم، قابلیت کنترلپذیری این تابشها در سطوح انرژی و دز دقیق. این دو ویژگی امکان میدهد تا بدون تماس فیزیکی یا نیاز به مواد شیمیایی خطرناک، ویژگیهای مکانیکی، حرارتی و حتی الکتریکی مواد مهندسی تغییر یابد.
در فرایند تولید مواد کامپوزیتی برای صنایع فضایی یا خودرویی، معمولاً از ماتریسهای پلیمری تقویتشده با الیاف کربنی، شیشهای یا آرامید استفاده میشود. این ترکیبات گرچه سبک هستند، اما برای رسیدن به بالاترین حد خواص مکانیکی، نیازمند اصلاح ساختارهای درونی و بهبود در پیوندهای سطحی میان اجزای ترکیباند. در اینجاست که پرتودهی وارد میدان میشود.
پرتوهای گاما، معمولاً از منابع رادیواکتیو مانند کبالت -60 یا سزیم -137 حاصل میشوند و در دزهای مشخص، قابلیت نفوذ بالا و اثرگذاری یکنواخت بر کل حجم ماده دارند. این ویژگی آنها را برای فرآیندهایی چون پخت همزمان قطعه، بهبود اتصال میان لایهها، افزایش مقاومت در برابر حرارت یا حتی کنترل نرخ تبلور پلیمرها ایدهآل میسازد.
از سوی دیگر، نوترونها بهویژه در کاربردهای تحقیقاتی یا صنعتی خاص میتوانند با نفوذ به ساختار ماده، ایجاد نقصهای کنترلشده کرده و فرآیندهایی چون تقویت سختی یا بهبود هدایت گرمایی را تسهیل کنند. شتابدهندههای ذرهای نیز با امکان تنظیم انرژی پرتوها، اجازه میدهند تنها لایههای خاصی از ماده مورد اصلاح قرار گیرد، بیآنکه کل ساختار تحت تابش قرار گیرد.
به این ترتیب، فناوری پرتودهی در خدمت طراحی هدفمند خواص ماده قرار میگیرد: مادهای برای فضا که سبک است اما در دمای 1200 درجه کار میکند، یا شاسی خودرویی که در تصادف نمیشکند ولی وزن فلز را ندارد. چنین چشماندازی تنها با بهرهگیری از دقت و قدرت ابزارهای پرتویی ممکن شده است.
اجزای اصلی سیستم پرتودهی برای تولید کامپوزیتهای ویژه
هر سامانه صنعتی که از فناوری پرتودهی در تولید یا بهبود مواد کامپوزیتی استفاده میکند، از مجموعهای هماهنگ از اجزا تشکیل شده که نقش هر کدام در تضمین دقت، ایمنی و اثربخشی فرآیند حیاتی است. نخستین و مهمترین مؤلفه، منبع پرتوی است. این منبع میتواند یک چشمه رادیواکتیو مانند کبالت -60، یک راکتور تحقیقاتی برای تولید نوترون، یا یک شتابدهنده الکترونی یا پروتونی باشد که بسته به کاربرد انتخاب میشود.
دومین عنصر کلیدی، سامانه پایش و کنترل دز است. پرتودهی دقیق نیازمند سنسورهایی با حساسیت بالا و نرمافزارهایی برای پایش پیوسته میزان تابش، زمان مواجهه، و یکنواختی تابش در تمام نقاط ماده است. تجهیزات Dosimetry صنعتی از جمله پرکاربردترین ابزارها در این حوزهاند.
سوم، اتاق پرتودهی یا محفظه محافظتشدهای است که تابش در آن انجام میگیرد. این اتاق باید با دیوارههایی از بتن سنگین، سرب، یا مواد جاذب نوترونی پوشیده باشد تا از نشت پرتوی جلوگیری کند. طراحی این اتاق با در نظر گرفتن فاصله منبع تا ماده، قابلیت چرخش، و خنکسازی انجام میشود.
چهارم، سامانه حمل و جابهجایی دقیق قطعات در محیط پرتودهی است. بازوهای رباتیک، مسیرهای نقالهای، یا ماژولهای چرخشی، بسته به مقیاس تولید، برای جابهجایی دقیق و بدون وقفه استفاده میشوند.
پنجم، سامانه پایش ایمنی پرتوی برای کارکنان و محیط است که شامل دزیمترهای شخصی، هشداردهندههای پرتو، و تهویههای مخصوص برای اطمینان از سلامت محیط کار میباشد.
و در نهایت، زیرساختهای نرمافزاری برای طراحی فرآیند پرتودهی (simulation) و تحلیل ساختاری پس از پرتودهی نیز بخش جدانشدنی این سامانهها هستند. ترکیب این اجزا، چارچوبی امن، قابلاطمینان و دقیق برای استفاده از انرژی هستهای در خدمت مهندسی مواد کامپوزیتی فراهم میآورد.
فرآیند کلی پرتودهی در تولید مواد کامپوزیتی ویژه
فرآیند پرتودهی برای تولید یا بهبود مواد کامپوزیتی ویژه در صنایع فضایی و خودروسازی، ترکیبی از مهندسی دقیق، برنامهریزی پرتوی، و کنترل کیفی مستمر است. این فرآیند معمولاً با طراحی ماده هدف آغاز میشود: انتخاب نوع رزین، نوع الیاف تقویتی، نسبت اجزاء و ساختار نهایی مورد نظر. پس از آن، تحلیل پرتویی ماده بهصورت عددی و شبیهسازی انجام میشود تا دز مطلوب، نوع تابش، و هندسه بهینه تعیین گردد.
در مرحله بعد، اجزای کامپوزیتی یا قطعه مونتاژشده بهصورت خام یا نیمپخته وارد محفظه پرتودهی میشوند. این فرآیند میتواند برای پخت نهایی رزین، بهبود اتصال الیاف به ماتریس، کاهش تخلخل، یا تغییر خواص مکانیکی انجام گیرد. تابش گاما معمولاً بهصورت یکنواخت از چند جهت انجام میشود، در حالی که پرتوی نوترونی یا شتابدهندهای ممکن است بهصورت نقطهای یا لایهای اعمال گردد.
در طول پرتودهی، دزیمترهای تعبیهشده بر روی نمونه و داخل محفظه، بهطور پیوسته میزان تابش جذبشده را اندازهگیری کرده و به سامانه مرکزی گزارش میدهند. در صورت انحراف از برنامه، فرآیند متوقف و اصلاحات لازم انجام میشود.
پس از پایان پرتودهی، قطعه برای مدت کوتاهی در محفظه خنثیسازی نگهداری میشود تا از نظر پایداری پرتوی، ایمنی محیطی، و افت احتمالی خواص بررسی شود. سپس آزمونهای مکانیکی، حرارتی، میکروسکوپی و شیمیایی برای ارزیابی اثر پرتودهی بر ماده صورت میگیرد. دادههای حاصل وارد بانک اطلاعاتی مواد شده و برای اصلاح مدلهای طراحی مورد استفاده قرار میگیرند.
تکرار این چرخه بهصورت هدفمند و کنترلشده، امکان بهینهسازی دقیق مواد برای کاربردهایی خاص را فراهم میکند: مثلاً یک قطعه بال فضاپیما، پس از سه مرحله پرتودهی و آزمون، میتواند به خواص ایدهآل مورد نظر دست یابد. این فرآیند، در کنار دقت پرتوی، بر مبنای چرخهای علمی، ایمن و تکرارپذیر است که مهندسی ماده را از هنر به علم بدل میکند.
انواع کاربردهای پرتودهی در صنایع فضایی و خودروسازی
کاربردهای فناوری پرتودهی در تولید مواد کامپوزیتی ویژه، دامنهای وسیع را در دو صنعت پیشرفته هوافضا و خودروسازی پوشش میدهد؛ صنایعی که در جستوجوی حداکثر عملکرد، و در پی سبکسازی، کاهش مصرف سوخت، و افزایش ایمنی نیز هستند.
در صنعت هوافضا، پرتودهی گاما برای افزایش مقاومت حرارتی قطعات بدنه فضاپیماها، بخشهایی از ماهوارهها و پوششهای حفاظتی بهکار میرود. پرتودهی میتواند ساختار مولکولی پلیمرها را بازچینی کرده و مقاومت آنها را در برابر دمای بالا، پرتوهای کیهانی و شوکهای مکانیکی افزایش دهد. همچنین در توسعه کامپوزیتهای بازتابدهنده برای صفحات خورشیدی فضایی، پرتودهی یکنواخت، عامل کلیدی در کنترل ضریب انعکاس و دوام سطحی است.
در صنعت خودروسازی، پرتودهی برای بهبود خواص مکانیکی بخشهایی مانند سپر، شاسی، پوسته موتور و اجزای تزئینی داخلی استفاده میشود. مثلاً پرتودهی الکترونی قطعات ترموپلاستیکی موجب افزایش مقاومت در برابر ضربه و کاهش تغییر شکل حرارتی در دمای بالا میشود. همچنین در قطعاتی که به کاهش وزن حساس هستند نظیر پانلهای درب، سقف یا گلگیر پرتودهی اجازه میدهد از مواد سبکتری با مقاومت بهبودیافته استفاده شود.
در هر دو صنعت، پرتودهی امکان اصلاح دقیق خواص ماده بدون افزودن مواد شیمیایی یا تغییر شکل ظاهری را فراهم میکند؛ مزیتی که بهویژه در تولید انبوه و استانداردسازی، اهمیت حیاتی دارد.
همچنین در کاربردهای خاص مانند ساخت پرههای توربین، تجهیزات مکانیکی متحرک در خلأ، یا قطعات تحملکننده فشار در فضا، پرتودهی موجب کاهش پدیدههای فرسایشی، تخریب اشعهای یا ضعف مکانیکی میشود.
حتی در حوزههای نوظهور مانند خودروهای برقی یا پهپادهای فوقسبک، استفاده از کامپوزیتهای پرتودهیشده در باتریپکها، صفحات اتصال یا اسکلت اصلی، مزایای رقابتی قابلتوجهی ایجاد کرده است.
مزایای فناوری پرتودهی نسبت به روشهای سنتی در تولید کامپوزیتها
در مقایسه با روشهای سنتی پلیمریزاسیون، سختسازی و مهندسی مواد، فناوری پرتودهی مجموعهای از مزایای بیرقیب را در اختیار مهندسان قرار میدهد. نخستین و برجستهترین مزیت، "عدم نیاز به تماس فیزیکی یا حرارت مستقیم" است. پرتودهی گاما یا نوترونی میتواند در دمای اتاق انجام گیرد و این امر در بسیاری از مواد حساس به حرارت، نظیر رزینهای مهندسی پیشرفته، مزیت بزرگی بهشمار میرود.
دومین مزیت، یکنواختی و دقت در اعمال انرژی است. برخلاف گرمایش یا واکنش شیمیایی، در پرتودهی میتوان انرژی را با دز مشخص و بهشکل همگن به تمام نقاط ماده منتقل کرد. این ویژگی باعث بهبود پیوندهای مولکولی، کاهش تنشهای درونی، و یکنواختی ساختاری میشود.
سوم، کاهش یا حذف افزودنیهای شیمیایی است. بسیاری از روشهای سنتی نیازمند کاتالیزور، تسریعکننده، یا پایدارکننده هستند که ممکن است برای محیط زیست یا سلامت انسان مضر باشند. پرتودهی این نیاز را کاهش داده یا حذف میکند و در نتیجه ماده نهایی ایمنتر، سازگارتر با زیستبوم و بازیافتپذیرتر خواهد بود.
چهارم، سرعت فرآیند است. پرتودهی معمولاً در چند ثانیه تا چند دقیقه انجام میشود، در حالی که روشهای سنتی ممکن است به ساعتها زمان نیاز داشته باشند. این مزیت بهویژه در خطوط تولید انبوه، منجر به افزایش بهرهوری و کاهش هزینه عملیاتی میشود.
پنجم، امکان اصلاح هدفمند خواص ماده است. با تنظیم دز پرتویی، میتوان دقیقاً آن خواصی را که مدنظر است از سختی و کشش گرفته تا هدایت گرمایی تقویت یا تضعیف کرد، بدون آنکه سایر ویژگیها آسیب ببینند.
در نهایت، ایمنی فرآیند و قابلیت کنترل دیجیتال آن، موجب میشود پرتودهی در محیطهای صنعتی پیچیده و با کمترین مداخله انسانی قابل اجرا باشد. این ویژگی، نهتنها خطرات انسانی را کاهش میدهد، بلکه استانداردسازی و تکرارپذیری فرآیند را تضمین میکند.
چالشها و محدودیتهای بهرهگیری از پرتودهی در تولید کامپوزیتها
با وجود تمام مزایای برشمرده، فناوری پرتودهی در صنعت کامپوزیت بیچالش نیست. نخستین و شاید مهمترین محدودیت، "زیرساختهای پرهزینه اولیه" است. ایجاد مراکز پرتودهی، اعم از تأسیسات ایزوتوپی یا شتابدهندهای، نیازمند سرمایهگذاری بالا، مجوزهای نظارتی سختگیرانه، و تخصصهای چندرشتهای است.
دوم، "محدودیت در اندازه قطعات" است. در حالی که پرتودهی برای قطعات کوچک و متوسط ایدهآل است، کاربرد آن برای قطعات بسیار بزرگ نیازمند طراحیهای خاص، منابع پرتوی با انرژی بالا، و مهندسی دقیق هندسه تابش است.
سوم، "آسیبهای بالقوه ناشی از پرتودهی بیشازحد" است. اگر دز تابشی دقیق تنظیم نشود، ممکن است موجب تخریب ساختار پلیمر، زردی، تردی یا کاهش خواص مکانیکی شود. این امر نیازمند پایش دقیق و آزمونهای پیشرفته کیفی است.
چهارم، "نگرانیهای ایمنی و زیستمحیطی" پیرامون کار با منابع پرتوی، بهویژه ایزوتوپهای رادیواکتیو است. هرچند پرتودهی صنعتی بسیار ایمن طراحی شده، اما در افکار عمومی هنوز با واهمههایی همراه است که نیازمند آموزش، شفافسازی و اقناع اجتماعی است.
پنجم، "فقدان استانداردهای بومی" در بسیاری از کشورها برای کاربرد پرتودهی در حوزه کامپوزیت، توسعه این فناوری را محدود میکند. در غیاب چارچوبهای قانونی مشخص، سرمایهگذاری بخش خصوصی و همکاریهای صنعتی کند خواهد بود.
با این حال، بسیاری از این چالشها با توسعه دانش فنی، همکاریهای بینالمللی، و سیاستگذاری هوشمندانه قابل غلبهاند. فناوری پرتودهی، علیرغم دشواریهایش، افقهای وسیعی برای تحول در صنعت کامپوزیت پیش رو دارد.
استانداردها و دستورالعملهای بینالمللی مرتبط با پرتودهی در صنایع کامپوزیتی
پرتودهی در تولید مواد کامپوزیتی، بهعنوان یک فناوری پیشرفته و پیچیده، نیازمند پیروی دقیق از استانداردها و دستورالعملهای بینالمللی است تا ایمنی، کیفیت و سازگاری محصولات تضمین شود. سازمانهایی مانند سازمان بینالمللی استانداردسازی (ISO)، کمیسیون بینالمللی حفاظت در برابر پرتوها (ICRP)، و آژانس بینالمللی انرژی اتمی (IAEA) از مهمترین نهادهای تعیینکننده چارچوبهای قانونی و فنی این حوزه به شمار میروند.
استانداردهای ISO مرتبط با پرتودهی، از جمله ISO 11137 که مربوط به استریلیزاسیون پرتو الکترونی است، مبنایی برای اطمینان از یکنواختی و دقت دز پرتویی فراهم میکند. هرچند این استانداردها ابتدا برای حوزه پزشکی تدوین شدهاند، اما بهصورت گسترده در صنایع کامپوزیتی نیز اقتباس و بهروزرسانی شدهاند.
ICRP چارچوبهایی برای حفاظت پرتویی انسانها و محیط زیست تعریف میکند و محدودیتهای دز پرتوی مجاز را تعیین مینماید. رعایت این محدودیتها در مراکز پرتودهی، از جمله موارد الزامآور است تا علاوه بر ایمنی کارکنان، سلامت جوامع اطراف تأمین گردد.
IAEA دستورالعملها و راهنماییهایی درباره طراحی مراکز پرتودهی، مدیریت ایزوتوپها، و فرآیندهای پایش پرتویی ارائه میکند که در کشورهای توسعهیافته بهعنوان پایه سیاستگذاریها و قوانین ملی تلقی میشوند. این سازمان همچنین بر همکاریهای بینالمللی در زمینه فناوری پرتودهی تأکید دارد.
علاوه بر این، استانداردهای خاصی نیز برای ارزیابی کیفیت مواد پس از پرتودهی، مانند ASTM F2459 برای مواد پلیمری پرتودهی شده وجود دارد که ویژگیهایی نظیر مقاومت مکانیکی، پایداری حرارتی، و دوام را هدف قرار میدهد.
در مجموع، پیروی از این استانداردها و دستورالعملها به تضمین کیفیت و ایمنی کمک میکند، و زمینهساز پذیرش گستردهتر مواد کامپوزیتی پرتودهیشده در صنایع حساس فضایی و خودروسازی خواهد بود.
پیشرفتهای نوین در فناوری پرتودهی مواد کامپوزیتی
دهه اخیر، شاهد پیشرفتهای چشمگیری در فناوری پرتودهی بوده است که روند تولید و بهبود مواد کامپوزیتی ویژه را متحول ساختهاند. یکی از مهمترین این پیشرفتها، توسعه شتابدهندههای ذرات با انرژی بالا و قابلیت تنظیم دقیق دز تابشی است که امکان اصلاح لایهای و موضعی ماده را فراهم آورده است.
در کنار آن، پیشرفت در مدلسازی رایانهای (simulation) و شبیهسازی فرآیندهای پرتودهی به مهندسان اجازه داده تا اثرات پرتوی مختلف را بر ساختار مولکولی مواد پیشبینی و بهینه کنند؛ امری که پیشتر بهشدت وابسته به آزمون و خطا بود.
توسعه فناوریهای جدید در منابع پرتوی، نظیر لیزرهای همتراز شده با اشعه نوترونی یا گاما، امکان تابشهای همگنتر و با نفوذ بیشتر را فراهم کرده است. این ویژگی در بهبود خواص مواد در ضخامتهای بالا و قطعات بزرگ کاربرد حیاتی دارد.
همچنین ترکیب فناوری پرتودهی با نانو فناوری و افزودن نانوذرات تقویتی، منجر به تولید کامپوزیتهایی با ویژگیهای مکانیکی و حرارتی بینظیر شده است؛ موادی که هم سبکی فوقالعاده و هم مقاومت بالا را دارا هستند.
در زمینه ایمنی، پیشرفت در سیستمهای پایش لحظهای تابش و استفاده از هوش مصنوعی برای کنترل دقیق فرآیند، باعث افزایش ایمنی و کاهش خطاهای انسانی شده است. این امر در صنعت فضایی که کوچکترین نقص میتواند هزینههای گزافی داشته باشد، اهمیت دوچندانی دارد.
از سوی دیگر، تحقیقات روی پرتودهی ترکیبی، مثلاً استفاده همزمان از اشعه الکترونی و نوترون، افقهای نوینی در مهندسی کامپوزیتها گشوده است که انتظار میرود در سالهای آینده به تولید صنعتی برسد.
آیندهشناسی و توصیهها برای توسعه فناوری پرتودهی در مواد کامپوزیتی
با نگاهی به روندهای کنونی و نوآوریهای آتی، آینده فناوری پرتودهی در تولید مواد کامپوزیتی، روشن و پرامید به نظر میرسد. پیشبینی میشود که در دهههای پیش رو، شاهد ادغام بیشتر فناوری پرتودهی با هوش مصنوعی، اینترنت اشیاء (IoT) و فناوریهای پیشرفته کنترل کیفیت باشیم که امکان کنترل و بهینهسازی بیوقفه و هوشمند فرآیند را فراهم میآورد.
از منظر سیاستگذاری، توصیه میشود کشورها و صنایع پیشرو، سرمایهگذاریهای بیشتری در ایجاد زیرساختهای پرتودهی، توسعه نیروی انسانی متخصص، و همکاریهای بینالمللی انجام دهند. بهویژه توجه به تدوین استانداردهای بومی و همکاری در تبادل فناوری، میتواند زمینه را برای ارتقاء این فناوری مهیا سازد.
در حوزه تحقیق و توسعه، تمرکز بر استفاده از پرتودهی برای تولید کامپوزیتهای چندمنظوره با قابلیت خودترمیمی، مقاومت بالا در برابر اشعه کیهانی، و عملکرد چندگانه، چشماندازی جذاب برای آینده است. همچنین، بهکارگیری فناوری پرتودهی در فرآیندهای بازیافت و بهبود مواد بازیافتی، به عنوان راهکاری پایدار و اقتصادی بسیار مورد توجه خواهد بود.
از سوی دیگر، توسعه فناوریهای پرتودهی قابل حمل و کوچکمقیاس برای استفاده در محیطهای دورافتاده یا درون خط تولید، از جمله اولویتهایی است که میتواند کاربردپذیری این فناوری را بهطور چشمگیری افزایش دهد.
همچنین ایجاد آگاهی عمومی و بهبود فرهنگ ایمنی پیرامون فناوریهای هستهای، از جنبههای کلیدی توسعه پایدار و موفقیتآمیز این فناوری در صنایع پیشرفته به شمار میرود.
نمونههای کاربردی موفق در صنایع فضایی و خودروسازی
در سالهای اخیر، نمونههای متعددی از موفقیت فناوری پرتودهی در تولید مواد کامپوزیتی در سطح جهانی به ثبت رسیدهاند که نقشی تعیینکننده در ارتقاء عملکرد و کاهش هزینهها داشتهاند.
در صنعت هوافضا، شرکتهای بزرگ هواپیمایی یا شرکتهای سازنده ماهوارهها، میتوانند از تکنولوژی پرتودهی گاما برای تولید قطعات سبک و مقاوم بدنه هواپیما استفاده کنند که علاوه بر کاهش وزن، افزایش طول عمر مفید قطعات را به دنبال خواهد داشت.
در خودروسازی، خودروسازان بزرگ میتوانند از پرتودهی الکترونی برای افزایش مقاومت و دوام قطعات ترموپلاستیکی و کامپوزیتهای تقویتشده استفاده کنند. این فناوری، به ویژه در تولید قطعات خودروهای برقی، نقش کلیدی در افزایش کارایی و ایمنی خواهد داشت.
علاوه بر این، استارتاپها و شرکتهای نوظهور در حوزه مواد پیشرفته، با بهرهگیری از فناوری پرتودهی موفق به ساخت کامپوزیتهای مقاوم در برابر آتش، ضربه و شرایط محیطی سخت شدهاند که کاربرد آنها در پهپادها، تجهیزات نظامی و خودروهای مسابقهای روزافزون است.
مواردی از بهرهبرداری این فناوری در صنایع فضایی کشورهای پیشرفته آسیایی و اروپایی نیز موجود است که با سرمایهگذاری در پژوهشهای پایه و کاربردی، افق جدیدی برای تولید متریالهای فوقالعاده گشودهاند.
جمعبندی
فناوری پرتودهی در تولید مواد کامپوزیتی ویژه، پلی است میان فیزیک هستهای و مهندسی پیشرفته مواد که توانسته است انقلابی در صنایع فضایی و خودروسازی رقم زند. این فناوری، با استفاده از تابش کنترلشده گاما، نوترون یا الکترونی، قابلیتهایی فراهم میآورد که در روشهای سنتی تحقق آنها دشوار یا غیرممکن است.
در این مسیر، بهبود خواص مکانیکی، حرارتی و شیمیایی مواد، کاهش زمان فرآیند تولید، و افزایش ایمنی و سازگاری محیطی، از جمله دستاوردهای ملموس و قابللمس پرتودهی هستند. هرچند چالشها و محدودیتهایی نیز وجود دارد، از جمله هزینههای اولیه بالا و نیاز به رعایت دقیق استانداردها، اما روند رو به رشد فناوری و پیشرفتهای نوین، افقی روشن پیش روی توسعه آن قرار داده است.
نمونههای موفق صنعتی و کاربردی در سطح جهانی نشان میدهد که این فناوری نه تنها جنبههای تحقیقاتی دارد، بلکه در خط تولید و بازارهای رقابتی نیز به اثبات رسیده است. آینده این حوزه به سرمایهگذاری هوشمند، توسعه نیروی انسانی متخصص، و ایجاد زیرساختهای ایمن و پایدار وابسته است.
تلفیق فناوری پرتودهی با دیگر فناوریهای نوین مانند هوش مصنوعی و نانوفناوری، چشماندازی از مواد کامپوزیتی هوشمند، مقاوم و چندمنظوره به ما عرضه میکند که میتواند سنگ بنای نسل آینده صنایع پیشرفته باشد. این چشمانداز، نویدبخش عصری است که در آن مواد مهندسی، نه تنها پاسخگوی نیازهای امروز، بلکه مبدل به راهگشای چالشهای فردا خواهند شد.