احیای صنعت با عصای دانشبنیان / شرکت دانشبنیان ایرانی، رقیبی نوظهور برای غولهای لعاب خارجی
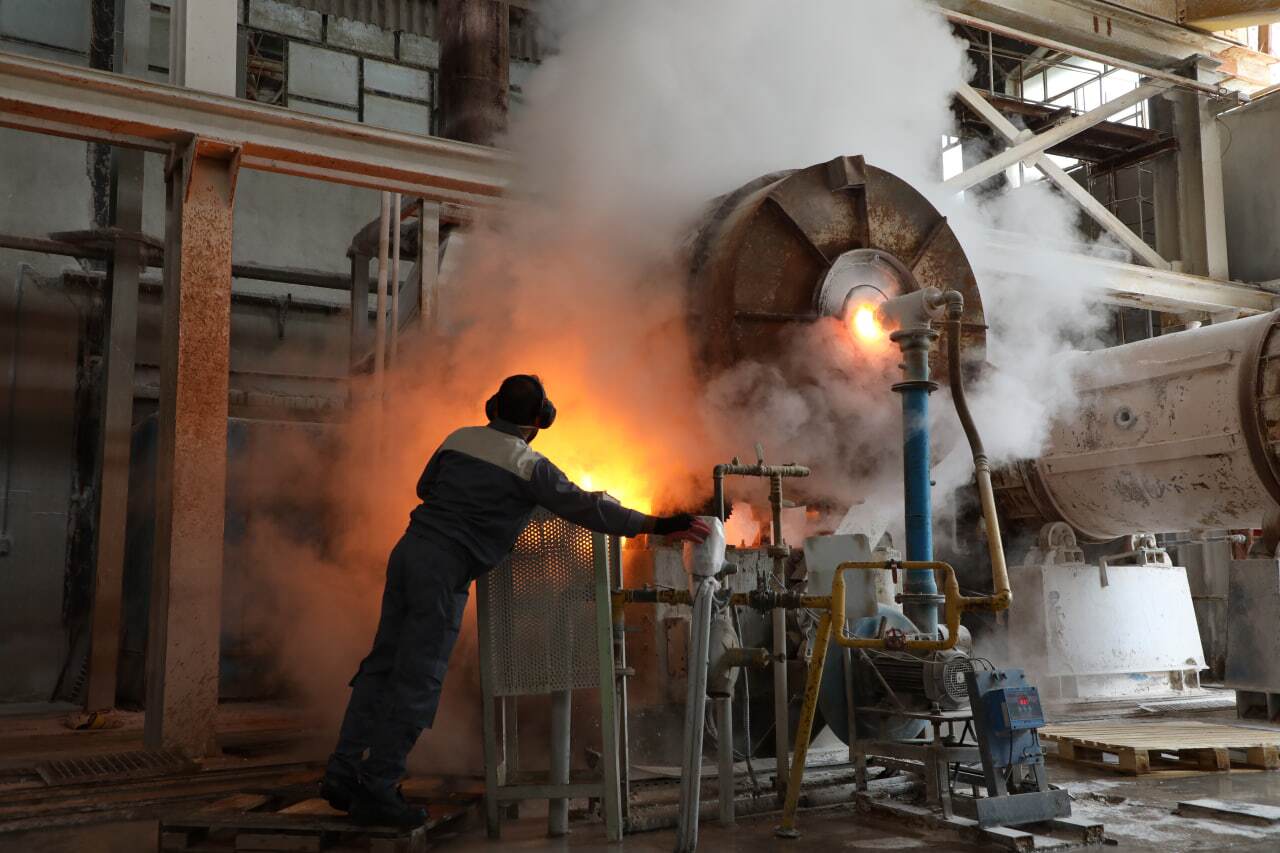
به گزارش خبرنگار دانشگاه خبرگزاری دانشجو، فاطمه کتابی؛ به دنبال رهنمودهای مقام معظم رهبری در خصوص آشنایی نخبگان و دانشجویان با دستاوردهای علمی و فناورانه کشور، معاونت علمی و فناوری و اقتصاد دانشبنیان ریاست جمهوری دردولت سیزدهم ضمن برگزاری تورهای علمی برای نخبگان، اقدام به برگزاری سلسله تورهای فناورانه برای خبرنگاران و راویان رسانهای کشور نیز کرده است. در ادامه با یکی از شرکتهای...
به گزارش خبرنگار دانشگاه خبرگزاری دانشجو، فاطمه کتابی؛ به دنبال رهنمودهای مقام معظم رهبری در خصوص آشنایی نخبگان و دانشجویان با دستاوردهای علمی و فناورانه کشور، معاونت علمی و فناوری و اقتصاد دانشبنیان ریاست جمهوری دردولت سیزدهم ضمن برگزاری تورهای علمی برای نخبگان، اقدام به برگزاری سلسله تورهای فناورانه برای خبرنگاران و راویان رسانهای کشور نیز کرده است. در ادامه با یکی از شرکتهای دانشبنیان کاشی و سرامیک مستقر در استان فارس آشنا میشوید.
یک کارخانه کاشی و سرامیک که در سال 1365 شروع به کار کرد، سالها سودده بود، اما از سال 1390 به دلیل واردات زیاد با مشکل روبرو شد و تا مرز ورشکستگی پیش رفت. اما در سال 1399 با کمک دانشبنیانی و نوآوری، این کارخانه احیا شد و بدون نیاز به هیچ دستگاه جدیدی، در سال 1400 به سود 5 میلیاردی، در سال بعد به 10 میلیارد و امسال به 40 میلیارد تومان سود خالص رسید. همچنین 150 نفر در این کارخانه مشغول به کار شدند.
شرکت دانشبنیان ایرانی، رقیبی نوظهور برای غولهای لعاب خارجی در دنیای کاشی و سرامیک، لعاب حرف اول را میزند؛ مادهای که گرانی آن، گاه تولیدکنندگان را به ستوه میآورد. اما خبر خوب اینجاست که شرکت دانشبنیان، با تولید لعابهای باکیفیت، گامی بلند در جهت خودکفایی و قطع وابستگی به نمونههای خارجی برداشته است. این شرکت که سابقهای درخشان در تولید لعاب کاشی دارد، در سالهای اخیر با تمرکز بر تحقیق و توسعه، سه محصول جدید به نامهای شوگر، وتروزا و گرانیلیا را به بازار عرضه کرده که با استقبال چشمگیر صنعتگران مواجه شده است. شوگر، لعابی با نامی شیرین، که یادآور دانههای ریز و درخشان شکر است. این محصول، جایگزینی ایدهآل برای نمونههای خارجی بوده و کیفیت و زیبایی خیرهکنندهای به کاشیها میبخشد. وتروزا، لعابی خاص برای پخت سوم کاشی است. در این مرحله، طرحهای سفارشی به کاشی اضافه میشود و لعاب وتروزا، جلوهای بینظیر به این طرحها میبخشد. گرانیلیا، نسل جدید لعاب دانه شکری، با فرمولاسیونی نوین، ظاهری مدرن و جذاب به کاشیها هدیه میدهد.
افتخارات دانشبنیانی نادر رضاییمنش، مدیرعامل این شرکت با اشاره به دانشبنیان شدن این سه محصول در سال 1402 گفت: این شرکت، اولین و تنها تولیدکننده لعاب در ایران است که موفق به اخذ تأییدیه دانشبنیان برای محصولات فروخته شده خود شده است. فاطمه مغیوری، مدیر تحقیق و توسعه شرکت، در تکمیل این صحبتها افزود: ما مفتخریم که به عنوان یک سازمان نوآور در رده شرکتهای دانشبنیان قرار گرفتهایم. این دستاورد، حاصل تلاش بیوقفه تیم تحقیق و توسعه شرکت در جهت ارتقای کیفیت و ارائه محصولاتی منحصر به فرد به مشتریان است. نوآوری بدون توقف اما داستان این شرکت با دانشبنیان شدن این سه محصول به پایان نمیرسد. به گفته مغیوری، در این شرکت، نوآوری و ارتقای کیفیت، روندی مستمر دارد. فرمولاسیون تمامی محصولات به طور مداوم بازنگری و اصلاح میشود تا بهترین کیفیت به مشتریان ارائه شود. با اتکا به این رویکرد، شرکت به عنوان رقیبی قدرتمند در عرصه تولید لعاب، گامی بلند در جهت خودکفایی و قطع وابستگی به نمونههای خارجی برداشته و نویدبخش آیندهای روشن برای صنعت کاشی و سرامیک ایران است.
مغیوری در مورد پروسه تولید محصولات دانشبنیان این شرکت تصریح کرد: «شوگر، گرانیلیا و وتروزا همه اصطلاحا حوزه کاربری متفاوت دارند، اما از یک پروسه تولیدی به نام دانهبندی میگذرند.
درحالت عادی، زمانی که فریت (اصلیترین محصول شرکت) تولید میشود از کوره وارد بیگ بگ شده و با کیسههای یک تُنی به کارخانه مشتری ارسال میشود. محصولات دانهبندی محصولاتی ویژه هستند و ما یک ارزشی را خلق کردیم؛ یعنی این فریت در مرحله دانه بندی تبدیل به اعداد مشخص میشود، زیرا روی الکهای متفاوت، دانه بندیهای مشخص دارد. این را که مشتری از ما میگیرد بدون هیچ تغییری مصرف میکند پس برای او خیلی حائز اهمیت است که دانه بندی مورد تأییدش باشد و در طول زمان، دانه بندی حفظ شود.
شرکتهای خارجی این محصول را تولید میکردند و شرکتهای ایرانی تولید کننده این محصول به طراحی اولیه دست پیدا کرده بودند، اما نتوانسته بودند ثبات دانهبندی را حفظ کنند و مشکلات زیادی برای مشتریان ایجاد میکردند. ضمن این که این شرکتها به دلیل این که خصوصی هستند محصول را با قیمتهای مشابه خارجی در بازار ارائه میکردند.» تولید «پیگمنت جوهر دیجیتال» برای اولین بار در خاورمیانه
مدیرعامل این شرکت دانشبنیان در ارتباط با محصول جدید این شرکت گفت: محصولی در دست تحقیقات با پیشرفت حدود 40 درصدی داریم که تولید پیگمنت جوهر دیجیتال برای اولین بار در خاورمیانه است. شرکتهای سرآمد دنیا در تولید این محصول که اسپانیایی و ایتالیایی هستند آن را با قیمت خوبی (کیلویی دو یورو یا بیشتر) میفروختند. ما هم روی این تحقیق کردیم. الان ما با قیمت یک یورو هم که بفروشیم، باز حاشیه سود ما از تمام محصولاتمان بیشتر است. چون رقیب نداریم.
تا قبل از سال 1390 پیگمنتی که در کاشی و سرامیک تولید میشد دانه درشت بود و روی کاشی و سرامیک چاپ میشد. همین شرکتهای پیشرو در دنیا این فرآیند جوهر و رنگ را عوض کردند. پیگمنت را از دانه درشت و قدیمی به صورت جوهر دیجیتال به بازار ارائه دادند. ما قبلا 250 پیگمنت و رنگ برای کاشی و سرامیک تولید میکردیم که دیگر منسوخ و متوقف شد.
سال 1399 طرح جوهر دیجیتال آماده بود که خواستیم با صد میلیارد تومان پیگمنت دانه ریز وارد کنیم و تبدیل به جوهر دیجیتال کنیم، اما نتیجه گرفتیم، چون پنج یا شش تولیدکننده جوهر در کشور هستند که پیگمنت خود را وارد میکنند آن را متوقف کردیم.
غیر از چهار کشور در دنیا هیچ کشوری تکنولوژی تولید پیگمنت جوهر دیجیتال را ندارد. ما کاری میکنیم که آن پیگمنتها که در جوهر دیجیتال مصرف میشود را تولید کنیم. کار بعدی ما در تبدیل به پروژه همین است. البته کار تحقیقاتی هم زمانبر است و هم ممکن است موفق نشود. ما قبل از آن چند پروژه تعریف کردیم و سه پروژه را موفق شدیم.
در ارتباط با کاربرد پیگمنت جوهر دیجیتال باید بگویم جوهره رنگ کاشی از پیگمنتها است. دانههای رنگی نانو هستند و آن ذرات نانو در دستگاه دیجیتال چاپ میرود و روی بدنه کاشی اعمال میشود.
در ارتباط با رنگ دانهها هم شش رنگ اصلی آبی، زرد، بژ، مشکی و قهوهای را داریم. این رنگها در سایر کاربردها بر اساس مواد شیمیایی و آلی هست. رنگهای ما معدنی هستند که با حرارت میتوانند با بدنه کاشی پیوند برقرار کنند.»
کاربری محصولات
مدیرتحقیق و توسعه این شرکت در ارتباط با کاربری سه محصول دانشبنیان این شرکت گفت: «کاشیهای سرامیک یک لایه ضخیم به نام بدنه دارد که خود شرکتهای کاشی هم طراحی و هم تولید میکنند. روی آن یک لایه میانی اصلاح کننده به نام انگوب است و روی آن یک لایه به نام لعاب میآید.
کیفیت محصول در اثر فعل و انفعالات و واکنشهای این سه لایه است، اما مشتری در بازار فقط لایه رویی را میبیند. همه کارهایی که در شرکتهای لعابسازی انجام میشود، برای زیبایی بصری روییترین لایه کاشی است که در اثر استفاده از انواع مختلف تزئینکنندههای سطحی روی لعاب (سطحیترین لایه) استفاده میشود.
این سه محصول کیفیت لعاب را ارتقا میدهد. یعنی لعاب را از حالت معمولی بیرون میآورد. مقاومت به سایش به آن میدهد، خوردگی رنگ را بالا میبرد، مثل یک لایه محافظ عمل میکند ضمن این که زیبایی بصری هم دارد. در واقع علاوه بر زیبایی باعث حفظ رنگ زیر نیز میشود و مقاومت به اصطکاک را هم حفظ میکند.» محصول جدید این شرکت که کاربردی غیر از کاشی و سرامیک دارد
مدیرعامل این شرکت، در ارتباط با محصولی از شرکت که کاربرد آن غیر از تولید کاشی و سرامیک است میگوید: «یک طرح جدید برای تولید سیلیکات سدیم با همین ماشین آلات داریم. سیلیکات سدیم دامنه وسیعی از مصرف دارد. در صنایع بهداشتی، چسب حتی بحث بریکت سازی فولاد، اما هدف ما این است که از سیلیکات جامد و مایع برسیم به سیلکات ژل یعنی سیلیکاژل را تولید کنیم.
سیلیکاژل یک رطوبت گیر است که در حال حاضر وارد میشود. قیمت مواد اولیه آن به کیلویی 10 هزار تومان هم شاید نرسد، اما با گرمی؟، کیلویی یک میلیون به فروش میرود و قیمت عمده آن کیلویی صد هزارتومان است. اینها ناشی از این است که ما تولیدکننده نیستیم. هدف ما ایجاد ارزش افزوده برای کشور است. ما در قسمت آزمایشگاهی هم به این رسیدیم، اما این که در صنعت برسیم هنوز کار دارد.»
روش محک محصولات و تعیین کیفیت رضاییمنش توضیح میدهند برای کسب اطمینان از کیفیت محصول سه مرحله تست انجام میشود تست آزمایشگاهی: اول محصول رو توی آزمایشگاه بررسی میکنیم تا ببینیم همه چیزش درست است یا خیر. تست صنعتی: بعد یک خط روی کاشی میکشیم و میبینیم که محصول چطور عمل میکند.
تست انبوه: در این مرحله 5 هزار متر از محصول را تولید کرده و از آن در کارخانه استفاده میکنیم. با این سه مرحله تست میتوانیم مطمئن شویم که محصولمان باکیفیت و قابل اعتماد است.
فرایندی بومیسازی محصولات مدیرعامل این شرکت دانش بنیان گفت: «ما محصول خارجی را مهندسی معکوس کردیم؛ این که با چه فشار و دمایی پخت شود (چون مواد اولیه را در کوره ذوب میکنیم) بعد در مخازن آب سرد میشود که تبدیل به شیشهخورده میشود. این که چگونه دانه بندی شود، بهره وری و راندمان چقدر میشود، بحث آلودگی و... که به چه روشی تولید شود که راندمان بالا برود و قیمت تمام شده کاهش پیدا کند ما رقیب زیاد داریم به خصوص در یزد که لعاب سازهای زیادی داریم که با تُناژ بسیار بالایی تولید میکنند. حدود 75 درصد کارخانجات کاشی و سرامیک در استان یزد است، اما ما تلاش میکنیم هزینهها را با اقدامات دانش بنیانی کاهش دهیم.»
مدیر تحقیق و توسعه نیز در اینباره افزود: «ما بعد از تحقیقاتی که در بازار انجام دادیم و متوجه شدیم مشتریان ما به چنین محصولات ویژهای نیاز دارند پروژه را استارت زدیم و نمونه خارجی توسط کارشناسان خود ما مهندسی معکوس شد و روی خیلی از محصولاتی که داشتیم، تستهای اولیه را انجام دادیم.
حوزه مشتری هم برای ما حوزه ارائه محصول و هم دانشگاه است. به واسطه این که کارشناسان ما به طور مداوم در حوزه مشتری خدمات ارائه میدهند، متوجه میشویم که چه پارامترهایی را باید رعایت کنیم.
از طرفی رقبای ما که در صنعت سرامیک جهان پیشتاز و غولهای صنعت هستند، برای ما محل آموزش و یادگیری مثل دانشگاه هستند. کارشناسان ما که آنجا بودند این تکنیکها را از آنها یاد گرفتند و به اینجا آورند و زمانی که طراحی شد مجدد به حوزههای درجه یک که اینها را استفاده میکردند، با شرکتهای کاشی و سرامیک پیشتاز ارسال کردیم، زیرا این محصولات عمومی نبود که همه استفاده کنند و زمانی که ما شروع به ساخت کردیم، چون در کل ایران فقط سه شرکت این محصول ویژه را استفاده میکرد، بعد از طراحی ابتدا در یک شرکت شروع کردیم که رضایت داشتند و مهم برای ما رضایت مشتری از ثبات این محصولات بود.
ما توانستیم با مراحل کنترلی که در پروسه تولید تعریف کرده بودیم ثبات این محصولات را هم جوری در نظر بگیریم که آنچه مشتری تحویل میگیرد مطابق نمونهای است که همان سه سال پیش تحویل گرفته است.»
آمار و ارقام مربوط به میزان تولید به گفته مدیرعامل این شرکت، تولید کاشی و سرامیک در کشورحدود 400 میلیون متر مربع در سال است که حدودا 400 هزار تُن لعاب نیاز دارد. تقریبا به ازای تولید یک متر مربع کاشی یک کیلو لعاب مصرف میشود؛ یعنی یک در یک.
حدود سه قسمت تولید لعاب در یزد کار میکنند. یعنی حدود 300 میلیون متر مربع، تقریبا 75 درصد در یزد هستند.
مدیرعامل این شرکت در ارتباط با میزان تولید این شرکت گفت: ما 100 هزار تُن بازار برای خود تعریف کردهایم. در این بازار ظرفیت اسمی ما 29 هزار تُن در سال بود. ما کورههای ثابتی داریم که با تعداد کارگر خیلی کم و مصرف گاز کمتر این مقدار تولید را انجام میدهند، اما تقریبا طی ده سال گذشته سلیقه بازار عوض شده و دیگر تنوع خیلی زیاد شده و حجم پایین آمده است؛ بنابراین کورههایی که ظرفیت تولید بالایی دارند از رده خارج شدند. چون برای سفارش کمتر از دو هزارتُن نمیصرفد؛ تولید ما در سال 1399 حدود 5500 تن، سال 1400، 7700 تن، سال 1401، 10500 تُن و سال 1402، 12500 تن بود. امسال 13250 تُن برای تولید خود تعریف کردهایم.
ما مرتب داریم به سمت جایگزینی مواد اولیه داخلی به جای خارجی میرویم. کاری که به بهره برداری رسید این بود که بتوانیم بخشی از پسماندهای جامد و معدنی کشور را بازیافت کنیم. ما در مجموعه خود ضایعات تیتان و کاتالیستهای تیتانی که در صنایع پتروشیمی و پالایشگاههای گاز به عنوان پسماند ضایعاتی، است را مثلا به میزان 400 تُن از کرمانشاه آوردیم. این پسماندها را به صورت رایگان گرفته و بازیافت میکنیم. قیمت تیتانی موجود در بازار حدود 150 هزار تومان است که ما حدود 200 تن را بازیافت کردیم که 50 تیتان با خلوص 80 درصد به دست آوردیم
چالشها به گفته مدیرعامل این شرکت، مشکلات بیشتر تأمین مالی است و در حال حاضر غیر از کارت بازرگانی (رفع تعهد ارزی که فرآیندها طی نشده بود) مشکلی نیست.
وی معتقد است همین که ظرفیت تولید دارد بالا میرود، تورم نیز بالا میرود. درست است که شرکت سود دارد، اما این سود پاسخگوی افزایش تولید و تورم نیست.
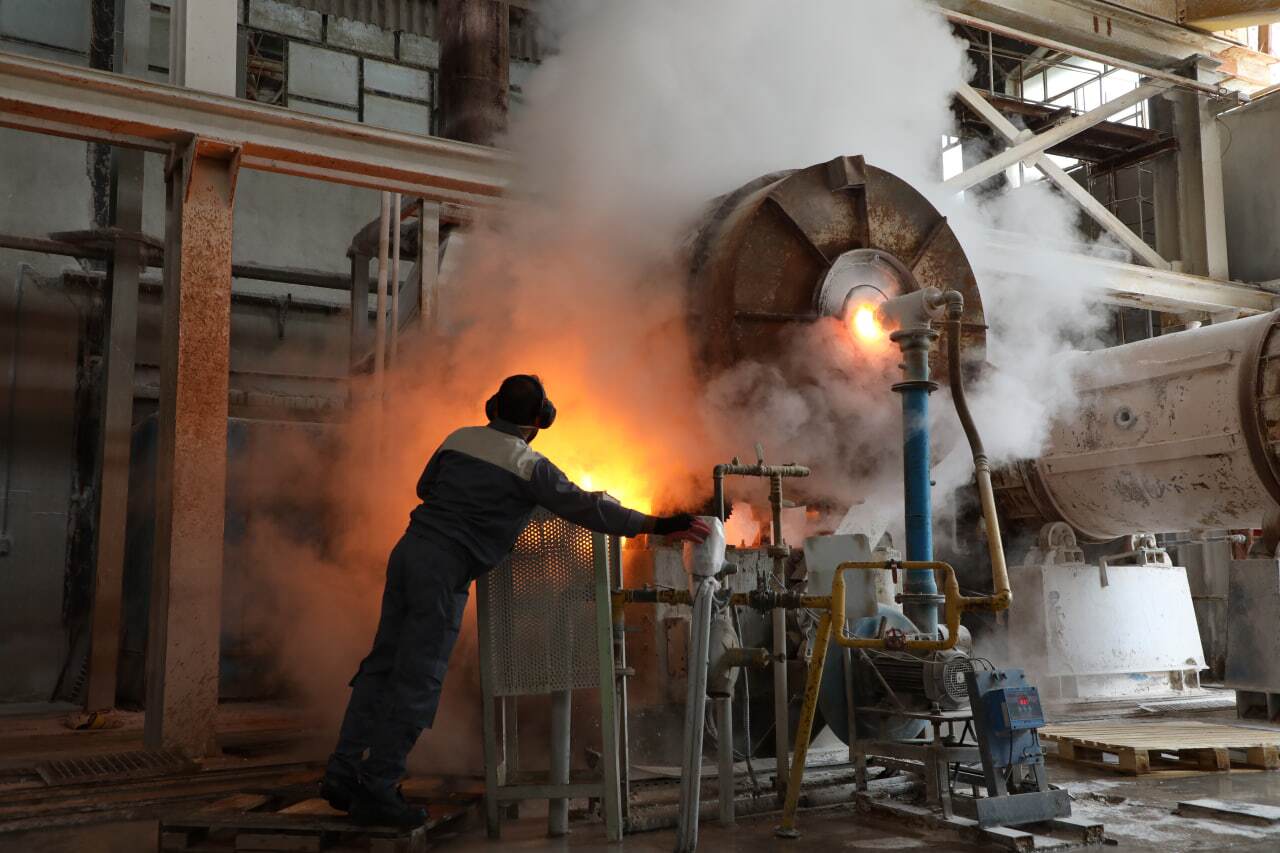
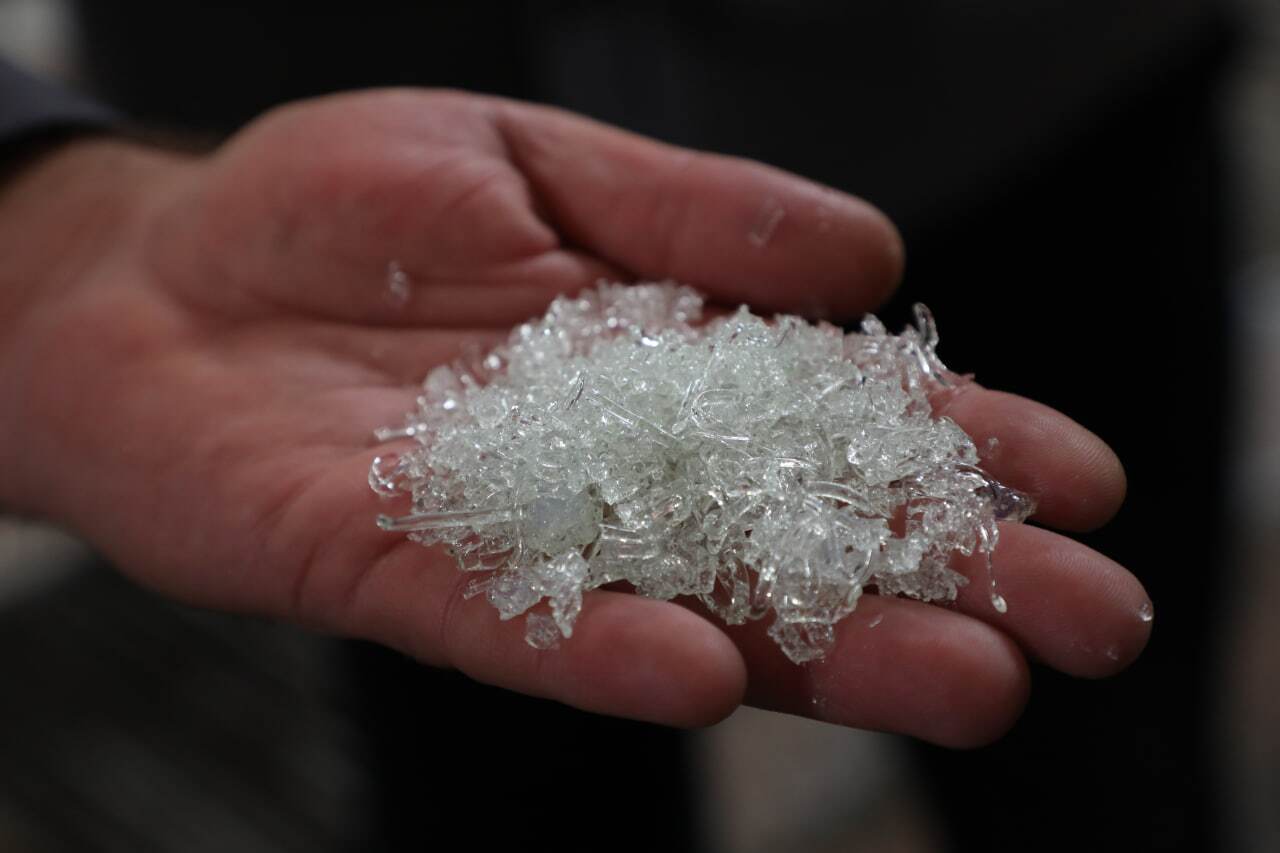
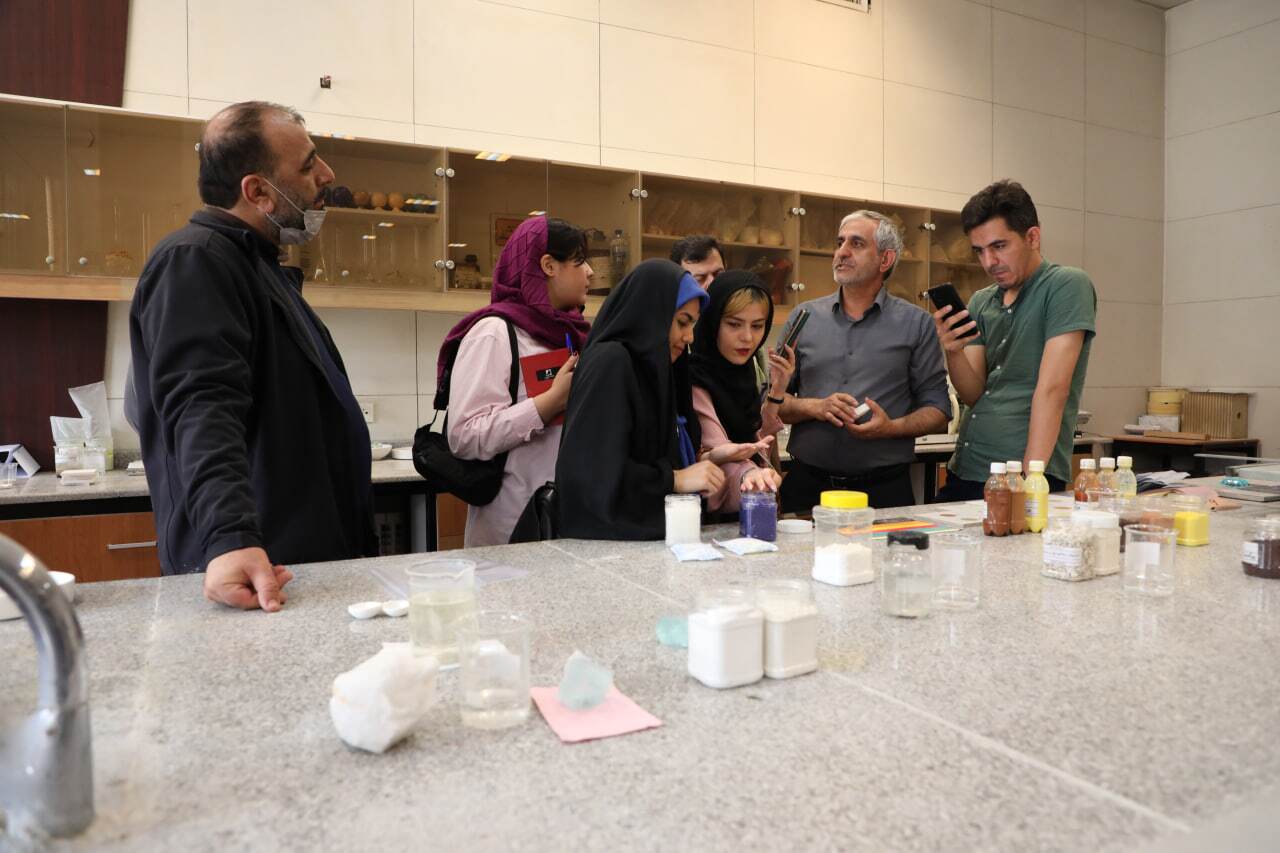